Pulse Width Modulation PWM controller. PWM is a technique in which the amount of current going in a circuit can be controlled by chopping the Direct current using a gate or transistor that is changing its duty cycle (on-off time) you should see this article flashing of LED using 555 IC. This article is about how you can control the speed of a DC motor using PWM motor controller.
This PWM circuit can be easily found in our daily life equipment like mobile chargers, laptop adapters, inverters, the power supply of desktop pcs, and in many other types of equipment in which steady low voltage is required.
We use DC motors like DC fans in many systems in our daily life. For example, to cool the system, in power supply, etc. Most of the time we have to control its speed according to the requirement.
There are many ways to do it. For example by inserting a series resistor to limit the current and hence limit the speed. But this is not a good way because in doing so, much of the power is wasted in the form of heat.
If we use any microcontroller, then this is an expensive method that is not affordable and suitable for small motors. That’s why we use PWM which has high efficiency and accuracy.
Concept of PWM controller fan :
Here we are providing a good way of DC motor speed control using PWM (Pulse Width Modulation). By changing the width of the square wave, speed can be changed. Speed depends on the duty cycle of the square wave. In this process, the switching frequency remains constant. PWM controller is also known as the dc-dc controller as it operates on dc to control dc.
What is Duty cycle?
Here is the concept of the duty cycle. Duty Cycle is the pulse duration divided by the pulse period. If the pulse has the same ON and OFF time, then its duty cycle will be 50%.
Greater the ON time of the pulse train, the greater will be the duty cycle. And hence greater will be the speed of the DC motor. In the below image you can see PWM with different duty cycles.
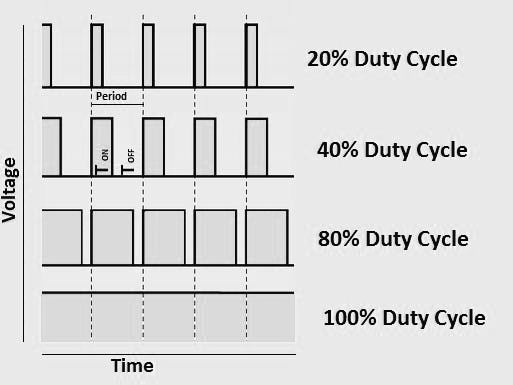
We are using IC 555 to generate a rectangle wave and to control the duty cycle. For more details on IC 555, see the datasheet.
Components:
-
- U1 555 IC
- R1 10k
- R2 10k
- R3 1k
- R4 1k
- RV1 100k potentiometer
- C1 10uF (25v electrolytic)
- C2 10nF
- Q1 IRFZ44N MOSFET (according to current requirement)
- D1 1N4148
- DC motor
Circuit Diagram:
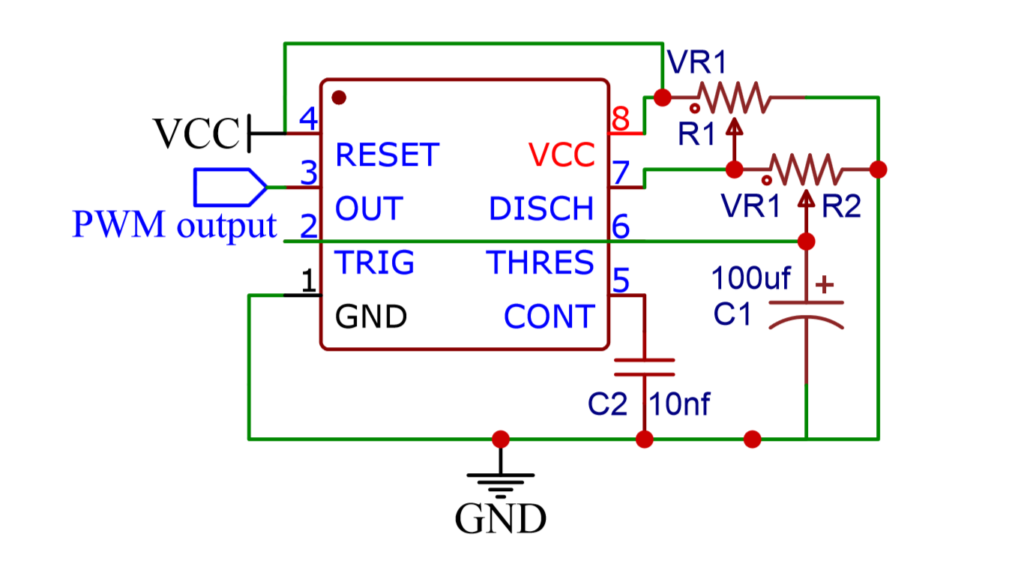
IC 555 is operating in astable mode. Frequency is dependent upon passive components-resistors and capacitors.
The speed of the motor can be changed by RV1 (potentiometer). if we increase the duty cycle, speed will increase, and vice versa. You can change the MOSFET according to your current requirement.
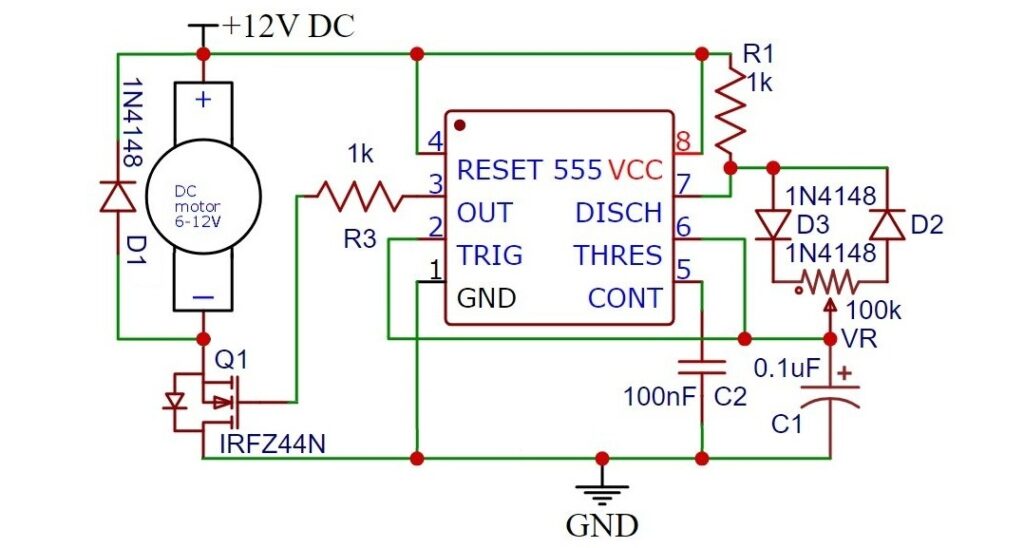
PWM controller circuit Explanation:
As shown in the above circuit the circuit contains a 555 timer, capacitor (10uf and 10nf), two potentiometers (10k & 20k), a MOSFET (IRFZ44N), a DC motor with diode protection (1N448 is used for high frequency switching applications.
Here I will not explain the working entirely as I have done in the previous article. To understand the working of 555 timer read this article.
The above circuit is a PWM controller 12V, it is the most efficient and simple circuit. It works better than the previous circuit which has two POTs also, here it has two diodes that control the direction of current flow. By PWM we vary the output current per unit time and average output voltage due to which the output power changes.
Connections:
- 555 timer is an 8 pin IC that can generate clock pulses of different frequencies.
- Pin 4 and 8 are connected to Vcc.
- There is a 1k resistor between pin 7 and 8.
- The two opposite diodes are connected to pin 7.
- The two fixed terminals of the 100k pot are connected to the two diodes.
- The variable terminal of the 100k pot is connected to pin 6.
- A 10uf capacitor is connected to the pin 6.
- the 100nf capacitor is connected to pin 5.
- Pins 2 and 6 are shorted.
- pin 3 gives PWM output to the gate of the MOSFET via 1k resistor (you should change it according to the requirements).
- The IRFZ44N is an N-channel MOSFET, having a high drain current of 49A and a low Rds value of 17.5 mΩ. It also has a low threshold voltage of 4V at which the MOSFET starts conducting. Hence it is commonly used with microcontrollers to drive with 5V.
- You can use any motor depending on your requirements and use the matching high-speed switching transistor.
working of the circuit:
In the PWM controller, 555 timer generates PWM signal, as the VCC is given to the circuit the capacitor c1 starts charging via resistor VR1 and VR2 once the capacitor gets charged to the threshold voltage (the voltage at which output changes to 0 or 1).
The transistor at pin 7 gets triggered which ultimately starts discharging the capacitor C1 the charging and discharging times are not the same as during charging both the resistors are involved whereas during discharging time only VR2 is involved which leads to a rectangle wave (not a square wave) it has unequal on and off-time.
Must watch this video for better understanding..
The frequency of output pulse depends on the RC time constant whereas the duty cycle (ON-OFF time) depends on the ratio of resistances of the two potentiometers.
If we change the POT (potentiometer) VR2 by keeping VR1 0Ω the minimum duty cycle will be 50%. whereas if both the POT are used then the minimum duty cycle can go below 10% to 5 %. The duty cycle may vary but the frequency of the output wave will remain constant.
By using this arrangement we can get our desired PWM signal of constant frequency.
How does the PWM signal control the speed of the DC motor?
The DC motor works on the principle of electromagnetism. when current flows through a conductor it produces an electromagnetic field. This field is also affected by the external magnetic field.
Rotor and Stator:
In a DC motor, there is a rotor and a stator. The rotor is made of electromagnets, they are the conductors wounded on iron metal. The stator is nothing but a pair of permanent magnets with opposite polarities fixed on the inner body of the motor. When current flows through the electromagnets they produce a magnetic field and are repelled by the stators the force produced by electromagnets is directly proportional to the current flowing through it and also the voltage across it.
So here comes the tricky point that when we give a high-frequency signal with a low duty cycle (ON time) the amount of current flowing through the coils gets directly affected and reduces. similarly when we increase the duty cycle, the current flowing through the coil increases leading to a very high speed of rotation.
precautions:
The frequency of the duty cycle should be high enough. If the frequency of the duty cycle is too low then it will cause a jerk to the motor and noise also. To avoid this, the frequency should be high enough for smooth rotations.
Even if the frequency gets high it should not get too high so that it crosses the switching speed of MOSFET (generally it never happens). A very high frequency can introduce a back emf in the circuit which can potentially harm the circuit. To prevent this designer should use diode protection (as shown in the circuit). If the inductive load is very high you must use the RC snubber circuit, to make other components safe.
thanks for reading our articles, you can comment down your doubts below in the comments section. Also, you can subscribe to our emails.
Hi there. I haven’t tried this circuit yet but it seems the schematic is missing the 104 cap connecting pins 1 and 2.
This is one of the few diagrams I found that uses a transistor to source instead of sink current to the motor. I needed the motor ground to be common ground and this ft the bill. However there are some problems with the diagram and circuit. The drain and source on the transistor are reversed (the built in diode is bypassing the transistor the way you show it). The dot on the NE555 should be on pin 1. 10uF makes for a VERY slow PWM. It should be more like 0.1 uF. The line connecting pin 2 to 6 is a bit confusing.
I have corrected that
Thank You
The Drain and Source of the MOSFET reversed. The entire Circuit Diagram turns wrong if you make a mistake with those 2 pins. Moreover, why connect the Motor to the Source of the MOSFET? If should be on the Drain of the MOSFET, on the high side.
I have updated the circuit you can check
Thank you